Rock-Breaker Automation
Together with colleagues from across the ICT Centre as well as CSIRO’s Division of Exploration and Mining, researchers from the Autonomous Systems Laboratory have developed technologies that will enable the effective and safe telerobotic control of mining equipment over distances of thousands of kilometres. Our technology has been proven on a Rockbreaker machine at Rio Tinto’s West Angeles iron ore mine, which was controlled by an operator over 1,000 km away in Perth.
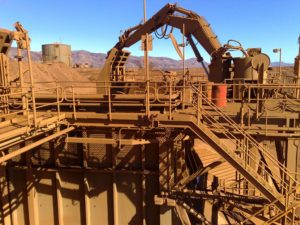
Rockbreaker at RioTinto's West Angelas iron ore mine, 110km west of Newman in Western Australia.
Rockbreaker at RioTinto’s West Angelas
The ability to remotely control mining equipment delivers benefits through removing people from hazardous and inhospitable working environments, as well as opportunities for increasing efficiency, productivity and profitability in mining. Traditionally remote operation in this industry has involved video being transmitted to a remote operator who makes decisions based on the visual evidence and responds by commanding the equipment to take action (i.e. tele-operation). Unfortunately, for many mining applications, this type of interface does not offer the human decision-maker sufficient situational awareness to effectively maintain manual production levels. This means that there has been, until now, limited economic benefit for remote operation of mining equipment (remote mining) over the traditional in-situ operation. Researchers from the Autonomous Systems Laboratory, together with colleagues from other groups within the ICT Centre and CSIRO’s Division of Exploration and Mining have developed technologies that provide higher levels of robotic control over the equipment (i.e. shared autonomy) and higher levels of immersion by delivering a wider range of more detailed information to the human operator in real-time.
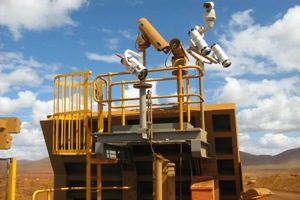
Stereo cameras looking down into ROM bin. Video cameras allow the remote operator to see into the rockbreaker bin.
Stereo cameras looking down into ROM bin
The first major test of this technology in action involved the remote operation of a rock breaker. This a large jointed arm fitted with a hydraulic hammer for smashing rocks dumped in the ore receptacle or ‘Run-of-Mine bin’ which are too big to enter the crusher. The project was commissioned by RioTinto Iron Ore Automation Group, and involved their primary rock breaker at the West Angelas iron ore mine, 110km west of Newman in Western Australia. The aim of the project was to demonstrate the feasibility of effective and safe telerobotic control over long distances (over 1,000 kms), as part of RioTinto’s long term plan to tele-operate their mining operations. The effective long-distance remote operation involves technical and cognitive challenges such as limited communications bandwidth, high latency, and lack of spatial and situational awareness for the operator. These challenges were addressed by developing technologies at both the local and remote ends of the system. We demonstrated that improving the intelligence of the control system at the remote end (e.g. Cartesian motion and collision avoidance capability) can mitigate the effects of latency, whilst mixed reality user interfaces (providing a combination of live video and 3D computer visualization) can improve the situational awareness for the operator.
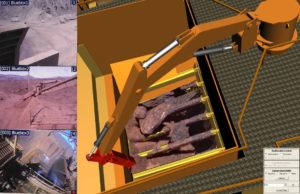
The mixed reality user interface combines live video and 3D stereo reconstruction
Mixed reality user interface combines live video and 3D stereo reconstruction
The rock breaker arm was fitted with a number of sensors to detect its pose in space and actuated by signals that bypass the existing remote-control system. PTZ (pan, tilt, zoom) cameras were fitted to poles on either side of the Run-of-Mine bin and a pair of high-resolution digital stereo video cameras were mounted below. All wiring was fed back to the local control room which was fitted with a computer to monitor and control the arm and process images from the cameras, an industrial PLC to monitor the site safety, and an Ethernet IO system to monitor and control the state of the hydraulic control system. From a user interface in Perth, this system allows the operator to “fly around” the rock breaker machine (via mouse commands) to inspect the over-sized rocks from different angles. Once they have established an appropriate breaking strategy, they can then deploy the rock breaker arm with a joystick. Trials during 2008 culminated in a production field trial which demonstrated that the telerobotic rock breaker system is safe and productive – indeed sometimes faster than traditional on-site operation. Importantly, it also integrates seamlessly with normal mine operations.
In 2008, this technology was commercialised by Transmin and is now called RockLogic
Publications
- Field and Service Robotics – The development of a telerobotic rock breaker
- Springer tracts in advanced robotics – Web-based tele-robotics revisited
- Patent – WO2010094057A1 Method and apparatus for providing a bit masked heartbeat signal
- Presentation – Remote Operations in Mining – “Mining in the Metaverse”