Excavator Guidance
This project developed and demonstrated a system that is able to simultaneously track the bucket of a mining excavator and map the terrain under the boom. Trials of a proof of concept system deployed on an excavator at the Blair Athol mine in central Queensland demonstrated that the system is able to generate dynamic Digital Terrain Maps (DTM) while tracking the location of the bucket teeth to within 10cm. Importantly, the trials also demonstrated that the sensors are able to survive over extended periods in the mining environment.
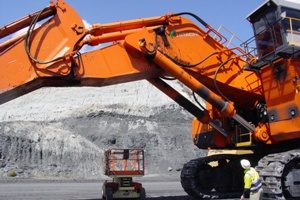
Excavator at Blair Athol Mine
One of the key developments made during this project is a novel self calibration technique. This technique is based upon the ability to use the a scanning range laser to simultaneously track the body and bucket of the excavator, and thus estimate the pose of the boom, stick and bucket joints, along with their respective angles. When coupled with a RTK GPS installed over the cabin, it is possible to translate the digital terrain map (DTM) under the boom into the mine coordinate system. With this technique, it is feasible that the system could be installed and calibrated in less than one day — thus not disrupting the normal operation of an excavator in production.
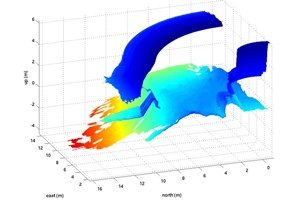
DTM Beneath Excavator
The most significant outcome of the project is the ability to provide dynamic DTMs underneath the excavator – i.e. maps that are updated in real-time. By subtracting the minimum DTM height from the initial DTM height it is possible to estimate how much material has been removed (reconciliation). This has an immediate benefit to the open-cut mining industry as it improves the accuracy of productivity measurements and provides the ability to drill down on the production data to see what has been mined and what has been left behind.
Once such a tracking system installed, it will be possible to overlay a real-time simulation of the excavator onto the dynamic DTM, providing a valuable visualization tool. This technology, referred to as ‘augmented virtualization’, has application in ‘dig-to-plan’ operations and for tele-robotic control of the excavator.
ACARP Tech Report C14043 Accurate Guidance and Measurement for Excavators using a Laser Scanner