Load Haul Dump (LHD) Automation
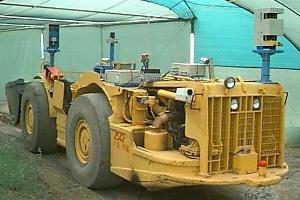
The LHD navigation system was first tested on a vehicle
operating in a simulated mining tunnel on the QCAT site.
Our solution involved placing a number of sensors on the LHD, including high speed scanning lasers, and developing software to control the machine. Unlike competitive systems, our automation system is based upon the principals of reactive navigation and opportunistic localisation - meaning that there is no prescribed path for the vehicle to take, but rather the system continuously reacts to the environment and tunnels walls and decides how to respond. As it drives the loader builds a map of the underground structure and compares it to an abstract mine map, evaluating the information before proceeding. The advantage of this system is that it is able to tolerate errors in position and lack of traction. If the vehicle is slightly off the expected path, it can quickly regain its normal course.
The LHD navigation system was first tested on a vehicle operating in a simulated mining tunnel on the QCAT site.
An LHD is a mid-sized (up to 60 tonnes) underground mining vehicle that loads, hauls and dumps (hence its name) metalliferous ore from an open stope (where there is broken rock) to a crusher or waiting truck to be transported to the surface. Since the roof of the tunnel in open stope areas is unstable, this type of operation presents a number of safety issues and provides a perfect opportunity for automation. Our aim in this project was to automate the haulage and dumping cycle for an LHD.
Our solution involved placing a number of sensors on the LHD, including high-speed scanning lasers, and developing software to control the machine. Unlike competitive systems, our automation system is based upon the principals of reactive navigation and opportunistic localisation – meaning that there is no prescribed path for the vehicle to take, but rather the system continuously reacts to the environment and tunnels walls and decides how to respond. As it drives the loader builds a map of the underground structure and compares it to an abstract mine map, evaluating the information before proceeding. The advantage of this system is that it is able to tolerate errors in position and lack of traction. If the vehicle is slightly off the expected path, it can quickly regain its normal course.
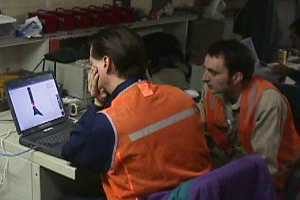
Researchers Elliot Duff and Jonathan Roberts testing
Researchers Elliot Duff and Jonathan Roberts testing
Our patented solution has been exclusively licensed to Caterpillar, who launched the product under the name MINEGEM in 2004 after extensive testing and refinement in a number of Australian metalliferous mines. The system has been sold around the world and is now in everyday use moving millions of tonnes of broken ore while operators sit safely in comfortable control rooms. Mines using the system have reported 40-60% productivity increases over the manual operation. This is in addition to savings in machine wear and tear that are achieved because the machine is driven to the manufacturer’s specifications rather than being subject to often arbitrary decisions about things like gear change by an operator.
History
The LHD project was split into 4 phases:
- 1996 – Feasibility Study (conducted between CSIRO, CMTE and ACFR at Mt Isa)
- 1999-2000 Research Project (under the control of CMTE and AMIRA, with RCT Global)
- 2001 Technology Transfer (a joint venture between Lateral Dynamics and Caterpillar Elphinstone to form Dynamic Automated Systems (DAS))
- 2002-2003 Commercialisation (contracts with CSIRO Launched on the 29th April 2003)
In 2009 Caterpillar released the commercial system called Minegem.
Today the system is called Caterpillar Underground Command.
System Architecture
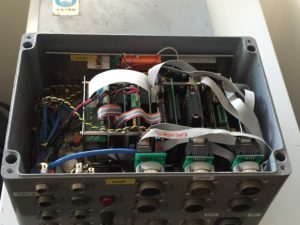
PC104 Computer with High Speed Laser Interface
The hardware was based upon industrial PC104 components. It consisted of a Pentium II Processor with a HSLI (High-Speed Laser Interface) board. This board was required to handle the lasers at the RS422 highest speed (please note, that this was before USB was commonplace). The significant advantage of the HSLI was that it was able to synchronise the acquisition of Lidar data with the steering encoders. The software consisted of LynxOS, DDX middleware and tclTK.
Publications
- Reactive navigation and opportunistic localization for autonomous underground mining vehicles
- Automation of an Underground Mining Vehicle using Reactive Navigation and Opportunistic Localization.
- US6694233 System for relative vehicle navigation
Videos
Presentation
- Autonomous Underground Loader for the 2008 IEEE/IFR Innovation and Entrepreneurship Award