Hot Metal Carrier Automation
Autonomous vehicles that operate with little or no human intervention are becoming increasingly common in factories, but in heavy industrial settings they are still rare, and there are currently no automated hot metal carriers (HMCs) in operation anywhere in the world. Hot metal carriers are 20 tonne forklift-style vehicles used in smelters to pick up crucibles of molten metal from pot lines and carry them to casting machines. Each crucible weighs about two tonnes and can hold up to eight tonnes of molten metal. The pot lines can be over a kilometre long. Apart from the physical difficulties of automating large vehicles, heavy industrial settings pose particular challenges such as spanning both indoors and outdoors, and having to deal with a range of issues such as dust and heat, strong magnetic fields, and the presence of people and other vehicles, all in an environment that is constantly changing
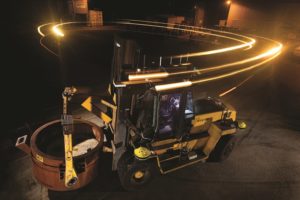
Forklift
Automating the process makes a safer work environment
We’ve created an autonomous hot metal carrier that is capable of conducting all the operations of a manned vehicle, as well as being able to monitor and manage its own hardware and software, and respond intelligently in the event of any issues or problems it may face. And since 2005 we’ve had a prototype working for many continuous hours across a range of conditions and environments at our industrial laboratory in Brisbane. We found that one of the big challenges was developing an accurate and robust localisation system that lets the HMC know exactly where it is at a particular moment. We based our localisation system on a range of technologies including a scanning laser rangefinder, pan and tilt zoom cameras, a steering encoder, and odometry that counts wheel rotations. The data from the combination of these sensors and a map of the site can pinpoint the location of the vehicle to within 20cm.
A safer and more efficient workplace
Our autonomous hot metal carrier offers a range of advantages over manually controlled vehicles, including removing humans from potentially hazardous environments for improved safety, as well as a range of other benefits such as an increase in operational efficiency, more consistent product delivery, and a reduction in operation and maintenance costs. Field trials of the core technologies have taken place at an operational production facility in Tasmania.
Publications
- Autonomous Hot Metal Carrier- Proceedings 2007 IEEE International Conference on Robotics and Automation
- Autonomous Hot Metal Carrier – Navigation and Manipulation with a 20 tonne industrial vehicle: : Proceedings 2007 IEEE International Conference on Robotics and Automation
- Vision-based operations of a large industrial vehicle: Autonomous hot metal carrier : Autonomous hot metal carrier Journal of Field Robotics Volume 25, Issue 4-5, pages 243–267, April – May 2008