Blast Hole Charging Automation
The aim of this project was to automate the charging process in underground mining. This process involves placing primer and detonators into holes drilled into the roof and walls of development drives, and filling the holes with liquid explosives. The vehicle to be automated (referred to as the Mobile Charging Unit) carries an emulsion pumping system, a primer/detonator assembly system and a hydraulic arm. CSIRO’s role in the project was to develop a hydraulic arm that is able to insert the emulsion hose into the pre-drilled holes.
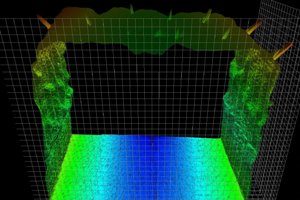
Blast Hole Charging
Underground mining involves four basic stages; drilling blast holes, pumping explosives into these holes (charging), blasting, and removing the broken rock (mucking). Blast hole charging involves the placement of a primer-detonator assembly at the end of a flexible hose and inserting the hose into a blast hole. By pumping liquid explosives (emulsion) into the hole, the primer-detonator assembly is pushed to the back of the blast hole (30 to 60m) leaving the trailing detonator wire. Once a ring of blast holes is filled, the detonator wires are joined and the rock blasted
In the past, blast holes were filled manually. More recently they have been filled with the assistance of a vehicle fitted with a hydraulic arm (called a Mobile Charging Unit). In 1998 CSIRO conducted field work at Cannington Mine in northwest Queensland to establish the feasibility of automating the blast hole charging process, and we later constructed a research prototype at our QCAT facility. To do this, we fitted the hydraulic arm of a shot-creting vehicle (a machine used to spray concrete onto walls) with computer controlled servos and encoders. A scanning laser mounted on the end of the arm was pushed back and forth though the tunnel to generate a 3D profile from which it was possible to identify most of the blast holes. By comparing the location of these blast holes to the mine drill plan, it was then possible to determine the absolute location of the vehicle.
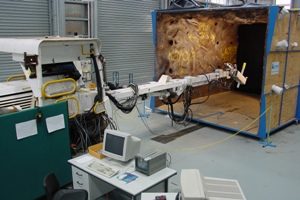
Research prototype hydraulic arm scanning inside a test tunnel at our QCAT site in 2000
Blast Hole Charging Prototype
Since neither the scanning laser nor the position of the arm is sufficiently accurate to insert the hose into each hole, it was necessary to complete the task of loading the holes using visual servoing. The advantage of visual servoing is that it does not need to know the absolute location of either the hose or the hole. The only requirements are that the arm is free to move in any direction and that both the hose and hole are visible at all times. The first requirement involves solving some complex control laws, while the second can be fulfilled via the appropriate placement of cameras and lights at the end of the arm and using the laser data to place the hose approximately 1m out from each hole. This system was successfully demonstrated at the end of 2001.
Publications
- IEEE Transactions on Automation Science and Engineering – Robotic explosive charging in mining and construction applications