Magnapods: Highly Flexible Inspection Robots
Magnapods are a class of bespoke high degrees-of-freedom autonomous inspection robots that are capable of navigating complex ferrous environments. Their flexibility allows them to access visually occluded pockets, thereby improving inspection coverage and quality over human inspectors.
In this endeavour, we are actively looking for research collaborators and industry partners in developing climbing inspection robots. (Contact: tirtha.bandy at csiro.au)
Inspecting Complex Infrastructure
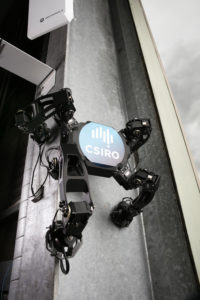
Maganapod climbing metal beam
Magnapod of quadruped configuration climbing a support structure
At CSIRO, we are developing bespoke platforms capable of inspecting infrastructure for condition monitoring, repairs, and maintenance. These high degrees-of-freedom autonomous platforms are capable of navigating complex environments and accessing visually occluded pockets in breathable and inert environments.
Aerial drones have proven to be a reliable option to reduce the cost of inspecting infrastructures. Our Hovermap payload mounted on an aerial drone is capable of autonomously building a high-resolution 3D model of the structure. However, additional platforms are required for complete coverage, close-range inspection, and defect mitigation. Our bespoke high degrees-of-freedom robots with controllable magnetic adhesion (Magnapods) enable long-term operation in the field enabling repeated and detailed coverage of the inspection area.
Magnapods are extremely useful in confined space inspection tasks where they have the potential to reduce operational time and cost by requiring less stringent preparation steps as compared to human entry. By keeping human operators out of confined spaces, a teleoperated robot significantly reduces the risk of adverse events involving human inspectors. Additionally, the inspection robot provides more comprehensive, quantifiable, repeatable and higher accuracy data which could be collected with a fraction of the operational logistics required of human inspectors.
Magnapod Inspection Robots
The robotic inspection platform has a variable number of limbs, depending on the task and the environment. The resulting high degrees-of-freedom makes the robot capable of achieving poses required to traverse complex confined space and structural environments. The inspection robot connected to a tether provides a data link as well as power for the robot. This allows the robot to operate for prolonged periods as it is not constrained by limited onboard power. In confined spaces, having the control computer outside the space, connected to the robot via a tether allows full control of the robot remotely. Overall, the tethered system provides the system with a higher degree of robustness, reliability and a retrieval mechanism if needed.
Video of the platform in operation:
Benefits
• Close range inspection in hazardous environments.
• Reduced downtime of operation.
• Significant economic gains in reducing the number of confined space workers required for each operation.
• Capable of achieving specific viewpoint as commanded by the operator.
• Capable of generating coverage statistics automatically.
Applications
• Inspecting hazardous confined space environments.
• Infrastructure and building inspection.
• Fuel and ballast tanks in maritime vehicles, including submarines.
Contact
For more information please contact: tirtha.bandy@csiro.au