The story of MyLM™ – from tracking space tech to tracking biomedical parts
CSIRO is behind some of the world’s biggest innovations.
Who would have thought that a team of engineers and astronomers studying black holes in space could lead to the invention of WiFi?
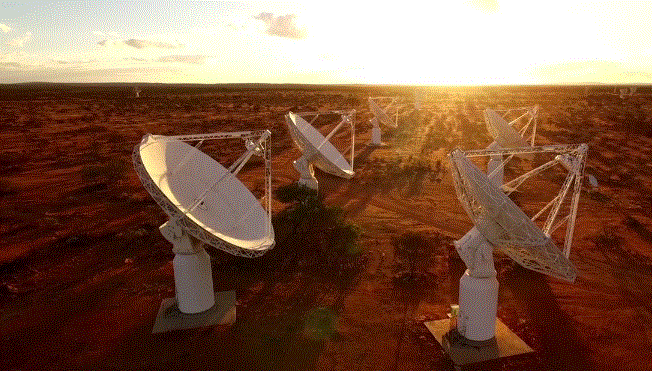
ASKAP dishes - screen shot from Puzzle video
The Australian Square Kilometre Array Pathfinder (ASKAP) is the world’s fastest survey radio telescope.
In the same corridors that WiFi was developed, CSIRO’s Astronomy and Space Science (CASS) team of scientists and engineers designed the world’s fastest survey radio telescope called ASKAP.
Mega science projects like the ASKAP radio telescope are at the cutting edge of engineering design, harnessing new technologies to build instruments that reveal more about the Universe. Along the way, engineers and scientists solve challenges with experimental ideas and designs that have the potential to be commercilaised, in collaboration with industry.
For instance, ASKAP comprises more than 6 million electrical components. To build the ASKAP telescope, tracking technology was created called ASKAP Hardware Tracker, that specifically tracked the lifecycle of each of its millions of components.
In the early stages of ASKAP design and production it was realised that the scale of the project with the sheer number of electronic hardware systems, sub-systems and components would result in configuration control and tracking soon becoming unmanageable without the assistance of some database-like system. The commercial offerings at the time, however, were either too limited or overly complex for the task. The database system needed to permit fast, straightforward capture of hardware details by a wide range of staff and contractors with varying levels of training and system knowledge. It also needed to provide an easy and flexible interface to interrogate the hardware data during the production, testing, commissioning and operational phases of the project.
Hardware Tracker follows the product lifecycle management path for each and every part of the telescope.
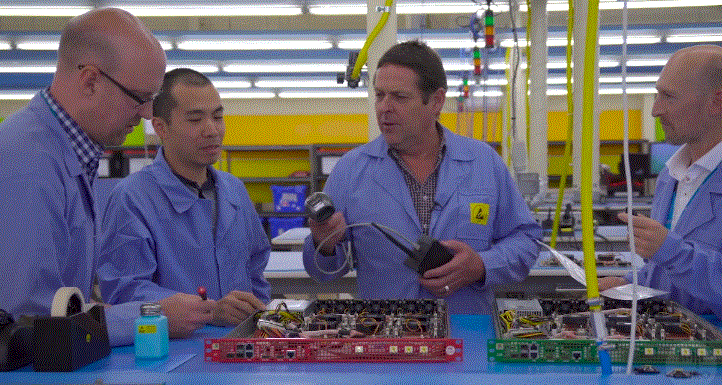
Puzzle Industries - screen shot from Puzzle video
Puzzle Precision, took on the challenge of piecing together the printed circuit boards and mechanical assemblies required for ASKAP: 20,000 of them, made from six million individual components.
The ASKAP Hardware Database was created by the ASKAP Engineering team as a means to at least initially capture the hardware details such as serial numbers, hardware revisions, modification and fault history as ASKAP production began and ramped up. Mobility, and barcode scanning of unique serialised ID’s on every part of the telescope, was a special feature of the technology. The software allows fast entry of hardware serial numbers through QR-code scanners and remote tablets and provides scripted assembly features to allow hardware components to be collected and grouped into sub-systems and systems. It permits levels of testing as well as enforced commissioning flows and fault/modification history recording.
The web-based system is built on open-source software products including MySQL, PHP and Python and grew considerably from its humble beginnings to a powerful tool that is still maintained and in use today by the operational crews at the instrument site in WA and engineering staff who provide remote debugging support from Sydney.
Applying the tech to a new industry
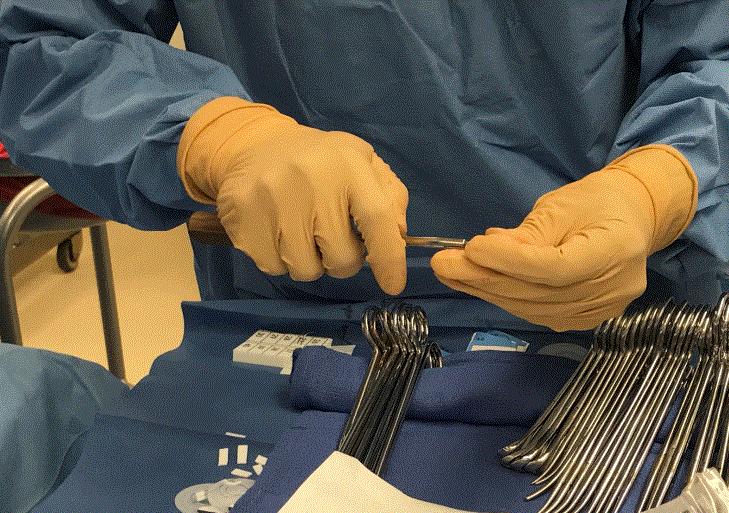
surgeon's hands in operating theatre
MyLM provides a medical device supply chain solution
Designer, Matt Shields saw that his customised Hardware Tracker – was limited only for use at the ASKAP project level. It could not be easily scaled or replicated for other large projects, which restricted its suitability for commercialisation.
The thing about CSIRO though, is its unique one-stop-research-shop value proposition that gives unprecedented access to multidisciplinary research teams working across a multitude of sectors. In a different part of Australia, a team of CSIRO’s additive manufacturing specialists were interested in applying the functionality of Hardware Tracker to managing the product lifecycle of their 3D printed parts.
And so, a decade later Hardware Tracker has evolved into the creation of MyLM™ – a truly scalable cloud-based tracking technology for industry.
CSIRO has developed MyLM™ to address supply chain problems for the Health and Life Science sectors. Over the last three years, Matt has worked alongside hospital staff to develop and refine the technology.
The MyLM™ enterprise solution is set for launch late 2020 at the Dreamforce event in San Francisco.